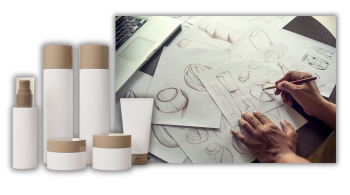
Plastic part design involves detailed plans that define the form and function of plastic components. Understanding how to design a plastic product in terms of material selection, adherence to standards, and other important details will help you balance eye-catching appearance with optimal performance.
When you partner with a plastic parts manufacturer, come ready to answer some critical questions for a successful collaboration. From production timelines to material selection, preparing to answer these questions will guide you to make the right choices, so you can achieve the optimal outcome for your plastic product design.
1. What Is the Part’s Intended Use?
A thorough understanding of the part’s intended use gives designers and engineers a better idea about how durable it needs to be. Describe the primary purpose of this part, along with specific functional requirements you have. Be sure to highlight both primary functions and secondary uses.
2. Will It Fit Onto a Bottle or Other Mating Device?
How will the plastic part integrate with other components? Answer this question by providing the device specifications like the shape, dimensions, and extra features that can impact the fit.
Other helpful information is the type of connection or interface you want the plastic part to fit onto. Describe connection points like locking mechanisms or threading. This level of detail gives the designer a better idea about allowances and tolerances they must consider to create a secure fit. The material of the plastic part must also be compatible with the material of the mating device to ensure proper functionality.
3. Do You Have the Specifications of All Other Mating Parts?
Information about more mating parts like bottles and other devices allows the manufacturer to consider your project’s broader context. It can improve the design process to ensure all-around compatibility. Provide the specifications like dimensions and tolerances of those parts. The more information you are able to provide, the more the designer will understand your needs and make recommendations on functionality and material selection.
4. What Is the Planned Material?
When the designer understands the plastic part’s functionality, they can better advise on the best material to use. Mention these variables to help determine the material for the plastic part:
- Functionality: Discuss the functional requirements, like having specific mechanical properties and the ability to withstand certain temperatures or chemical resistance.
- Aesthetics: Specify color requirements and surface finishing if the part’s appearance is essential, as certain plastics offer a more comprehensive range of aesthetic options.
- Regulatory Compliance: The material selection must align with regulatory compliance, especially for the pharmaceutical and food industries.
5. How Important Is Sustainability for the Use of This Part?
If sustainability is important to the overall packaging or this specific part, mention it from the start to ensure you select a material with eco-friendly characteristics. Sustainability extends to various processes outside of material selection. These include:
- End-of-Life Consideration: Consider materials that align with environmentally friendly disposal practices like recyclability. If this is an essential factor, you must pick a material that is widely accepted in recycling programs.
- Energy Efficiency: Some manufacturing processes are more energy efficient, having a lower environmental impact than others.
- Lifecycle Impact: The part’s longevity influences your material choices.Discuss its lifecycle, including whether it is a single-use item or should have the ability to withstand many uses.
6. What Are the Must-Have Features for This Part?
Plastic product design relies on structural integrity. Discuss the geometry of the part you require as a critical feature of the design:
- Aesthetics: Highlight the importance of the part’s appearance and how its construction should contribute to a visually appealing, cohesive design.
- Ergonomics: If users will interact with the plastic part, ensure the design prioritizes ergonomics for better user comfort and functionality.
- Manufacturability: Ensure the design is compatible with the manufacturing process to lower complexities for more efficient production. Draft angle and undercuts can all facilitate the plastic part’s molding.
7. Will It Require a Hermetic Seal?
Does the part need a seal that will serve as a contact-only seal or a seal that will make it airtight? A hermetic seal prevents air, gases, contaminants, or oxygen from getting into the container. Semiconductor electronics, optical devices, switches, and thermostats often use these seals to ensure proper functioning. This sealing can align with epoxy resins, metals, ceramics, glass, and plastics.
8. How Many Units Do You Need?
Estimate how many units you will need ahead of time. Start with a conservative estimate for new products, and scale up according to the market response. Take production capacity, lead time, and economic order quantity (EOQ) into account. EOQ principles will help to determine the optimal order quantity, lowering inventory holding and ordering costs.
9. Who Will Receive the Part?
Will you receive the part or will a contract filler receive the part? Clarify who will receive the part, which will impact the packaging, labeling, and potential presentation. If the part ships to a contract filler where it will assemble into a larger product, share this information to help the manufacturer understand integration requirements. Additionally, manufacturers may need to account for extra protection during transportation if the part ships to a third party.
10. How Quickly Do You Need the Part?
How soon do you need the completed part? Providing this information to your manufacturing partner gives them a clear understanding of your time requirements, allowing them to assess the feasibility of meeting that timeframe. Consider these factors:
- Your Project Timeline: Share your timeline with the manufacturer and point out critical milestones that may affect the deadline. Remember that design revisions may impact this schedule, too.
- Prototype Needs: If you need a prototype, discuss the timeframe for these iterations and how it fits into the overall project schedule.
- Shipping and Distribution: Needing to ship products to different locations will add to your project timeline.
Partner With The Plastek Group for Plastic Parts Manufacturing
Navigating the process of designing a plastic part requires a thoughtful approach to some critical questions. Clear communication is vital to the success of your plastic part manufacturing journey, helping ensure you receive parts that align with your project requirements and vision.
Molding the future since 1956, Plastek is a leader in plastic parts and packing manufacturing, with experience supplying numerous markets. We offer quality products and exceptional service. Contact our knowledgeable team to help you design and create the plastic parts that will best meet your application. Request a quote for your specific project needs or call us at 814.878.4400.