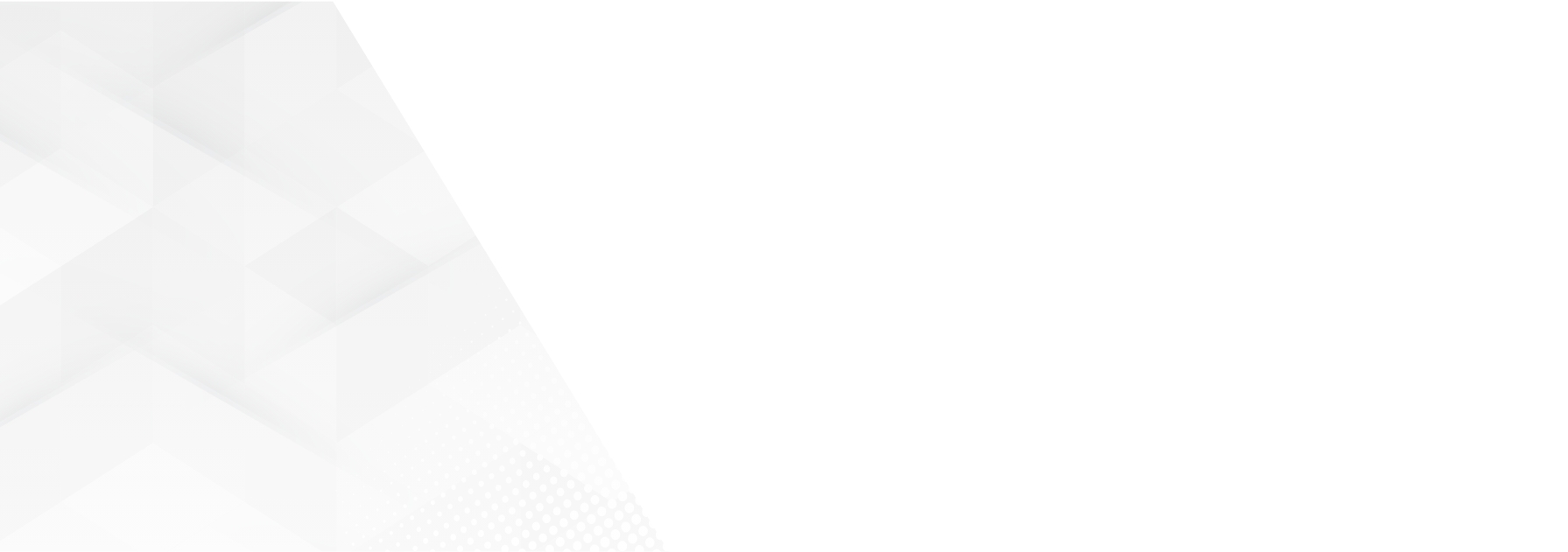
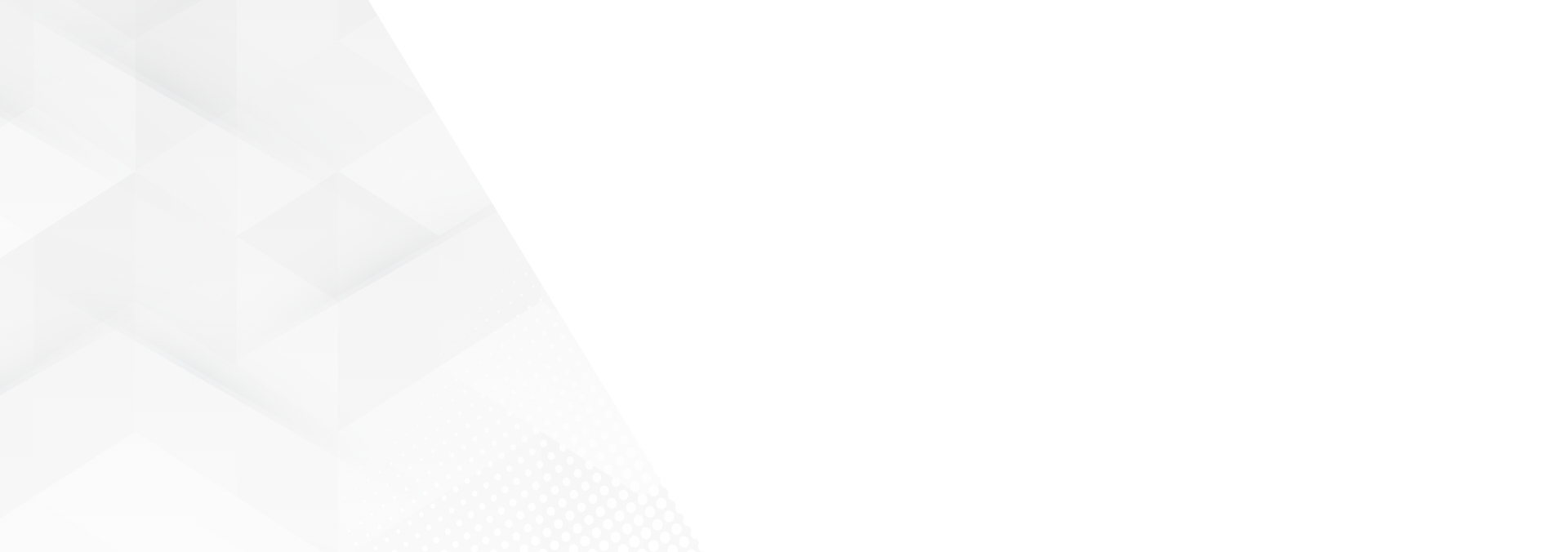
Components and Packaging
At The Plastek Group, our plastic design and manufacturing capabilities make us an excellent partner for all types of plastic products, including components and packaging. While these terms are often used interchangeably in plastic production, they have unique characteristics that set them apart.
Contact UsGuide to Identifying the Plastic Product Need
- Looking at the different facets of components and packaging can help you prepare for the design process and the decision-making that goes into these pieces. Regardless of what you’re looking for, The Plastek Group ensures your plastic products are high-quality and purpose-built.
- Is the product you’re seeking to manufacture, a Plastic Component, or a Plastic Package?
Is your plastic product need, a single part (component), or an assembly of parts (package)?
Navigate through the dropdown sections below for further comparisons of the two:
One of the core differences between rigid Plastic Components and Packaging is why you need them for your product.
- Plastic Components are parts or pieces that perform a specific function in your product design. These components are integral to a product’s functionality, like appliance parts, electronic device casings, or car interior components.
- Plastic Packaging is designed to protect, store, and transport products. A product with plastic packaging does not need the container or enclosure in order to function, but it makes the product more accessible and marketable. For example, plastic bottles make it easy to sell and use condiments. Other examples of plastic packaging include clamshell packaging, food containers, and blister packs.
- Plastic Components are engineered to perform specific functions like structural support or mechanical strength. Often, these components have to meet requirements for performance and durability to be used in a product. Stringent standards are especially common for automotive and aerospace components.
- Plastic Packaging serves the same function for any product — containing and protecting. Thanks to plastic packaging, you can prevent damage, contamination, and tampering with your product. While packaging can play a role in structural integrity, such as a plastic container for spreadable butter, its main function is preserving the integrity of the product.
- Plastic Components play an essential role in a product’s function, and the material needs to meet these functional demands. Your component may require a certain level of temperature resistance, distinct mechanical properties, electrical conductivity, or any other performance-related characteristic. Common plastics used for components include ABS, polycarbonate, and polypropylene.
- Plastic Packaging must meet certain performance characteristics as well, but in a different way. Packaging needs barrier properties to ensure moisture and oxygen can’t infiltrate the product and cause it to spoil. Other factors in material selection for packaging include cost-effectiveness, transparency, and moldability.
Most enterprises will have a budget to work with, and less expensive plastics help them produce more units of a given product. The transparency of plastic is
important for a couple reasons. Some products may need protection from light to maintain integrity and safety. Other times, you may require a transparent package
to see the product inside, like salad dressings and condiments.
Common plastic types for packaging include PET, PVC, HDPE, and PP. Certain packaging designs also need high moldability to make the design achievable.
At The Plastek Group, we use a series of manufacturing processes to achieve the ideal specifications for components and packaging.
- On the Plastic Component side of production, we typically rely on precision molding processes like injection molding and extrusion. The accuracy of these processes offers high repeatability, so all components align with your specifications. We can also achieve tight tolerances to ensure the component performs as it should.
- On the Plastic Packaging side, our team often mass-produces packaging designs with various molding techniques. We use injection molding for packaging as well as blow molding. Every process is highly efficient, allowing us to produce large batches on tight schedules. The ease of these processes also makes them incredibly cost-effective and excellent for keeping your budget in check.
Since components and packaging vary in their purpose and function, design considerations also vary widely between the two.
- When designing rigid Plastic Components, functionality takes center stage. The design needs to suit the function of the part and meet structural integrity requirements for performance. Additionally, the part must be compatible with the system or product it will integrate with.
When we partner with you to design a component, our team often works with complex geometries to achieve the right design. Custom features are also an essential aspect of component design. That’s why we don’t offer stock designs for components like we do for packaging. A turnkey design process is the best way to approach plastic components. - Plastic Packaging has very different design considerations compared to components. Functionality is certainly important in packaging design, but it is not the main priority. As long as the packaging protects its contents, it meets functionality requirements.Usability is also a valuable part of packaging design. Problems like a cap that’s hard to open or a seal that leaks can leave a negative impression on consumers. Your packaging should be designed thoughtfully for the product and how it’s used. For example, a plastic jar is an excellent packaging type for facial moisturizer, but it may not be the best choice for ketchup.
Packaging is the first impression that customers have about a product, making aesthetics another major consideration in design. Factors like shape, size, and color all contribute to the style of plastic packaging, and they can communicate subtle messages for a given brand. For instance, natural or eco-friendly products often have organic packaging shapes and colors like green and brown.